Simple gear train
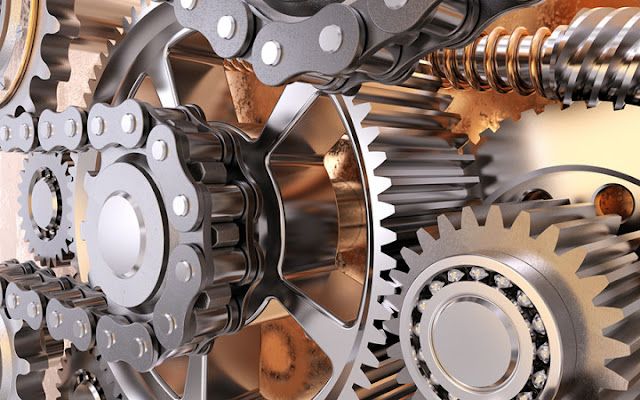
When there is only one gear on each shaft, as shown in Fig. 1, it is known as a simple gear train. The gears are represented by their pitch circles. When the distance between the two shafts is small, the two gears 1 and 2 are made to mesh with each other to transmit motion from one shaft to the other, as shown in Fig. 1 (a). Since the gear 1 drives the gear 2, therefore gear 1 is called the driver and the gear 2 is called the driven or follower. It may be noted that the motion of the driven gear is opposite to the motion of driving gear. Fig. 1. Simple gear train Let N 1 = Speed of gear 1(or driver) in r.p.m., N 2 = Speed of gear 2 (or driven or follower) in r.p.m., T 1 = Number of teeth on gear 1, and T 2 = Number of teeth on gear 2. Since the speed ratio (or velocity ratio) of the gear train is the ratio of the speed of the driver to the speed of the driven or follower and ratio of speeds of any pair of gears in the mesh is the inverse of thei...