Reverted Gear Trains
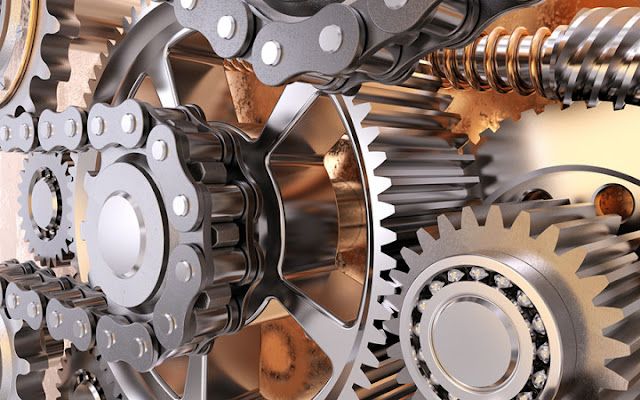
When the axes of the first gear (i.e. first driver) and the last gear (i.e. last driven or follower) are co-axial, then the gear train is known as reverted gear train as shown in Fig. 3. Fig. 3. Reverted gear We see that gear 1 (i.e. first driver) drives the gear 2 (i.e. first driven or follower) in the opposite direction. Since the gears 2 and 3 are mounted on the same shaft, therefore they form a compound gear and the gear 3 will rotate in the same direction as that of gear 2. The gear 3 (which is now the second driver) drives the gear 4 (i.e. the last driven or follower) in the same direction as that of gear 1. Thus we see that in a reverted gear train, the motion of the first gear and the last gear is al ike. Let T 1 = Number of teeth on gear 1, r 1 = Pitch circle radius of gear 1, and N 1 = Speed of gear 1 in r.p.m. Similarly, T 2 , T 3 , T 4 = Number of teeth on respective gears, r 2 , r 3 , r 4 = Pitch circle radii of re...