Vane pumps
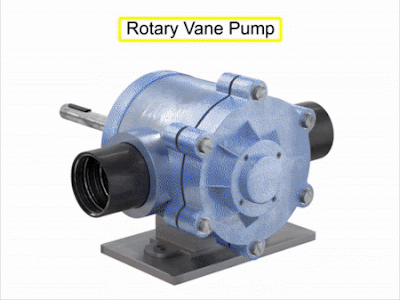
Vane pumps Gear pumps have a disadvantage of small leakage due to the gap between gear teeth and the pump housing. These limitations are overcome in vane pumps. The leakage is reduced by using spring or hydraulically loaded vanes placed in the slots of the driven rotor. Capacity and pressure ratings of a vane pump are generally lower than the gear pumps, but reduced leakage gives an improved volumetric efficiency of around 95%. Types: Vane pumps are available in a number of vane configurations including sliding vane, flexible vane, swinging vane, rotary vane, and external vane, etc. Each type of vane pump has its own advantages. External vane pumps can handle large solids. Flexible vane pumps can handle only the small solids but create a good vacuum. Sliding vane pumps can run dry for short periods of time and can handle small amounts of vapor. The vane pumps are known for their dry priming, ease of maintenance, and...