Mechanisms
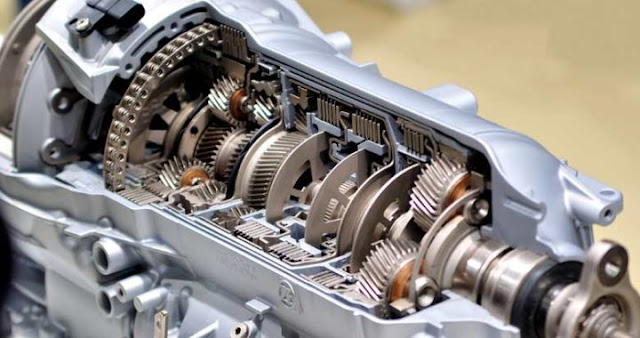
Mechanisms are essentially used for converting motion from one form to another. Mechanical actuation systems mainly consist of mechanisms. If a number of rigid bodies are assembled together in such a way that the motion of one causes constrained or predictable motion of the others, it is called a mechanism. Thus, a mechanism transmits and modifies a motion. The mechanism can be used for the following purposes: Transform linear motion into rotational motion (Example: IC engine) Transform a rotary motion into translating motion (Example: Cam and follower) Transform motion in one direction into another direction at right angles (Example: bevel gear or worm gear) Change (increase or decrease) and change the direction of the rotational speed of one drive to another (Example: gear trains) Figure 1. Linear to rotational motion transformation in IC engines Figure 2. Rotary to linear motion transformation in cam and follower Figure 3 Transformation of motion in one direction into another u...